In Praise of the 6-mm wrench, or “Say Hello to my Little Friend!”
Posted on Nov 4, 2019 in Featured | 2 comments
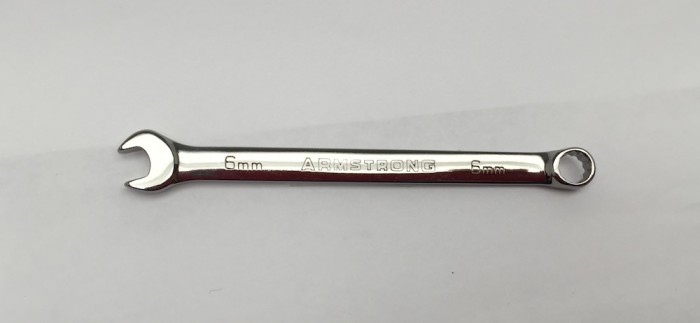
In the past year or so, I have been trying to assemble a complete set of hand tools, filling in the gaps and adding some tools I didn’t even know I needed. You can never have too many tools, right? Right?!?!
Wrenches are a simple thing, but in recent years, ratcheting wrenches, “cross force” designs and flex-head models have changed what you might find on store shelves and in toolboxes. Some of these innovations can come in quite handy. While I don’t need them all, the tool companies have made me feel like I do. Who am I to argue with their marketing?
I was raised by a machinist father who took great pride and stock in having the right tool for the job—and knowing how to use it. He was also a fan of American-made tools, something I really took to heart. I learned from my father the likes of how to tell a good ratcheting mechanism by feel, the signs of a well-crafted knurl in the handle and other indications of a quality tool. He showed me the differences between well-made tools that seem destined to last forever and those that were more or less disposable. And despite the chaotic condition of my cubicle at work (sorry, boss), the tools are always well organized, clean and easy to find—another legacy of the old man.
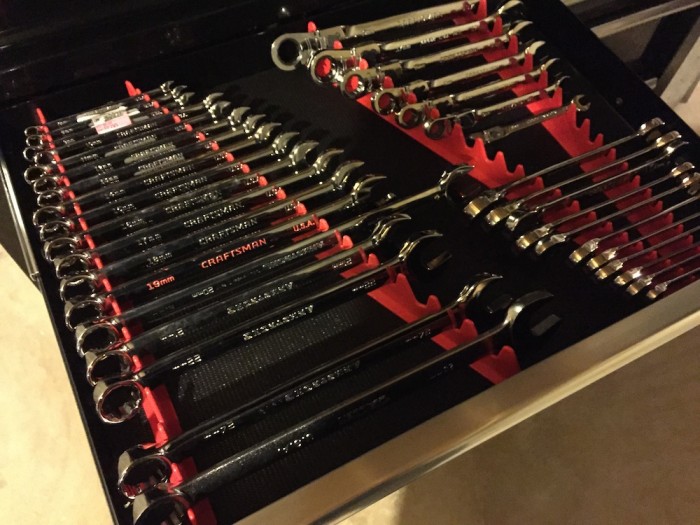
With that in mind, filling in the gaps included finding the last of the American-made Craftsman hand tools at local Sears stores and finding Armstrong, Allen and a few other tools from the likes of Cripe Distributing, an online seller of closeout tools with a great selection and reasonable prices—and many U.S.-made items.
Since I normally wrench on my BMW or our newer family cars, I completed my metric combination wrench from sizes of 32 mm all the way down to 6 mm, the smaller simply a more robust-looking companion to the typical wrench found in the bag of midget wrenches the tool sellers used to throw into a set to pad the number of tools included. It’s from Armstrong, a company with a long tradition of making high-quality tools in the U.S. As much as I wanted to complete the set, I wasn’t sure when I would need to use such a small tool, but my BMW gave me just the right task to put it to use.
Recently, I took on the job of replacing the rear shocks on my 2002 BMW M coupe. The car had just over 93,000 miles on it, the dampers were getting weak, and the shock mounts—a not uncommon BMW problem—were simply worn out, with the suspension making a disconcerting clunk over every bump, nook, cranny or pebble encountered on the road. It was well overdue, in other words.
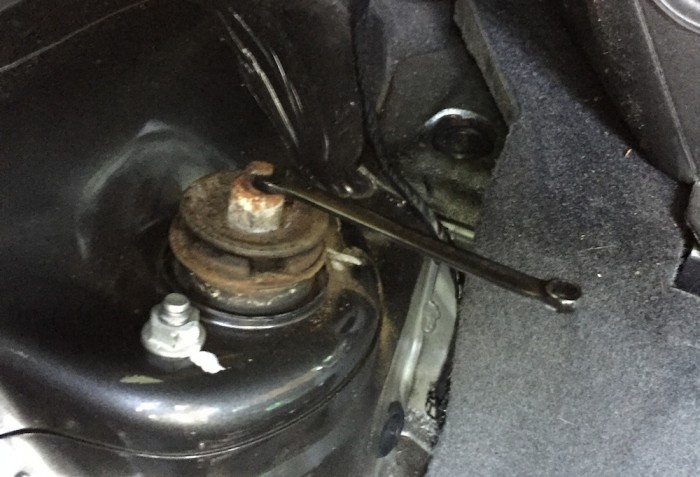
In the upcoming October issue of Hemmings Sports & Exotic Car, I’ve written up the details of how complicated BMW made getting to the shock mounts in the M coupe and similar Z3 coupe models, turning what should be a 10-minute job into a several-hour quagmire of trim and interior panel removal. Let’s just leave it at this: Officially, you need to remove the seat belts to get to the rear shock. The car has no back seat, so that absurdly means you need to remove the front seat belts to service the rear shocks. But, there are ways around that so that you don’t need to remove so many pieces, though it still requires an extensive amount of disassembly of the interior.
With all of that stuff out, the top mounting bolt on the threaded bar of the stock Sachs/Boge shock shaft has a 6-mm notch on top that needs to be held in place to remove the self-locking nut. The replacement Bilsteins instead use an internal hex key to keep the shaft from rotating when installing or removing the top nut.
For the first shock, which had a bit of corrosion on the threads, I tried the Channellock and Vise-Grip routine before essentially rounding off whatever was left of the 6-mm notch. I should add here that, despite listening to my father over the years, I don’t always figure things out that quick. To call myself a hack mechanic would be an insult to mechanics and hacks alike. Speaking of hacks, I need a hacksaw to finish the job, because, while I was going to toss the mount along with the shock, I would need the washer-like metal plates that go on the top and bottom of the mount and the rounded off notch was virtually ungrippable, even with the Vise-Grips.
Ultimately, I paid closer attention to the notch on the second shock and read the manual again where it specified the 6-mm size. It’s amazing the stuff they put in those books, isn’t it?
Armed with that tiny 6-mm combination wrench, I was able to remove the second shock with far less fanfare, and also avoid the nuclear option of having to use the hack saw.
GearWrench X-Beam’s (Open + Ratchet). Nirvana when you have to push/pull HARD on a 52 year old Chevy or 85 year old Ford.
Liked ’em so much I bought the metric also, just in case I have to push/pull HARD on a 10 year old VW!
Armstrong makes a Maxx Beam wrench set that is truly wonderful on the hands.