Gasoline Direct Injection: Fad or Future?
Posted on Jun 4, 2022 in Technology | 2 comments
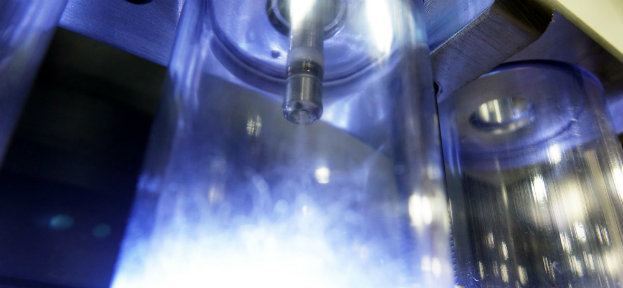
The internal combustion engine is 150 years old and its thermal efficiency – the amount of energy converted from combustion into mechanical work – is unlikely to achieve parity with emerging alternatives. For the performance enthusiasts among us, harboring anxiety over the future, you are not alone.
Although the internal combustion engine’s monopoly on automotive motivation may be over, the fun is not.
You do not need to run out and buy your last real performance car.
Not yet.
Automakers have been investing in internal combustion engines (ICE) for over a century and have produced more than one billion in the last 20 years. They are not giving up on the core technology that powers their products but several new technologies have emerged, enabling manufacturers to meet increasingly restrictive fuel economy standards.
Thermal efficiency has risen from around 15 percent in the Ford Model T to as high as 35 percent today. This 133 percent efficiency increase is positive and we have numerous developments to thank. For example, the Electronic Control Unit (ECU), material advances, turbocharging, and now gasoline direct injection (GDI). In fact, GDI is already well established, being part of Mazda Skyactiv, Ford Ecoboost, GM Ecotec powertrains.
In 2009, just seven percent of passenger vehicles sold in the United States were GDI equipped. Today, manufacturers are in continual transition to GDI and this year, approximately half of gas powered new cars sold in the United States will be GDI.
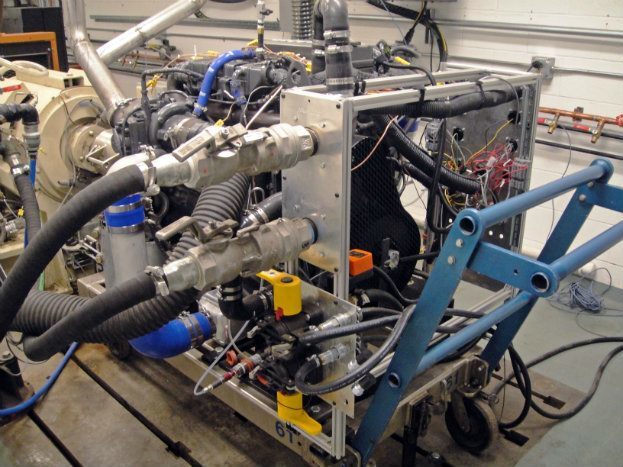
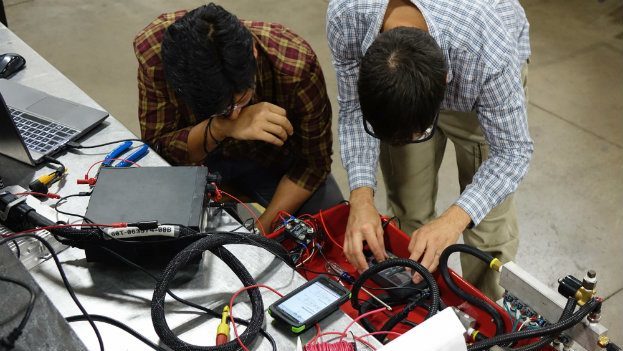
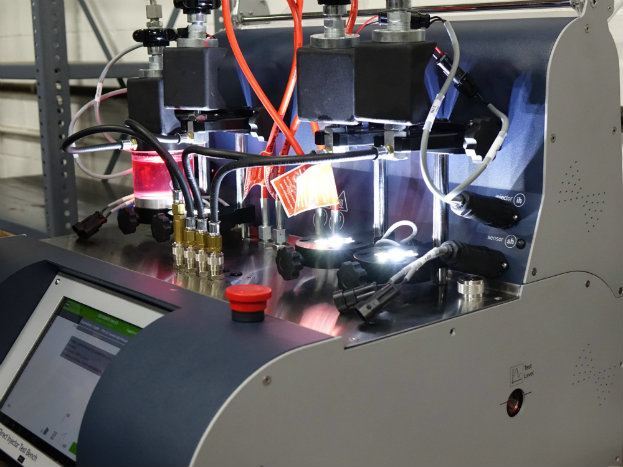
Gasoline Direct Injection is writing today’s chapter in the story of fuel delivery for internal combustion engines. It is the latest in a progression of technologies, each of which have moved the introduction of fuel closer to the point of combustion. The succession of fuel delivery technologies began with carburetion, progressed to single-point fuel injection (SPFI), developed into multiport fuel injection (MPFI), and has finally reached GDI.
Each technology was a significant advance over the last.
And while increasingly complex, unless you are an engineer at Bosch, Denso, or Eaton, you don’t need to know how to develop a GDI system to understand how one works.
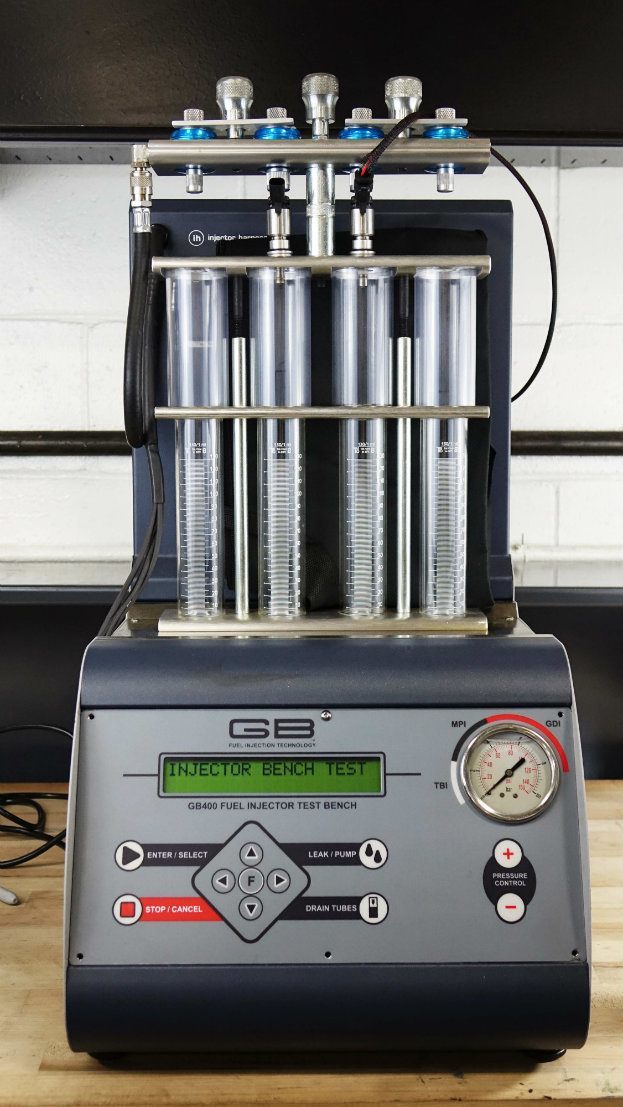
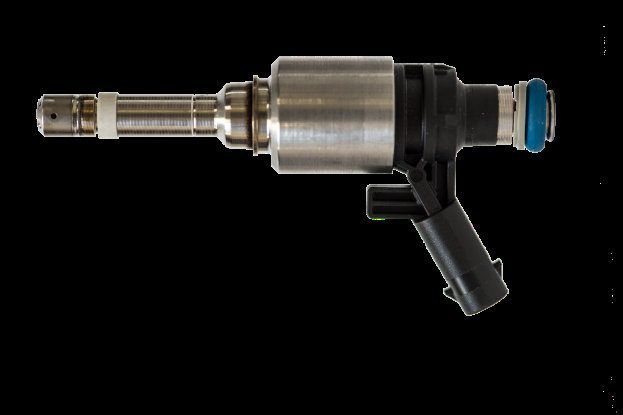
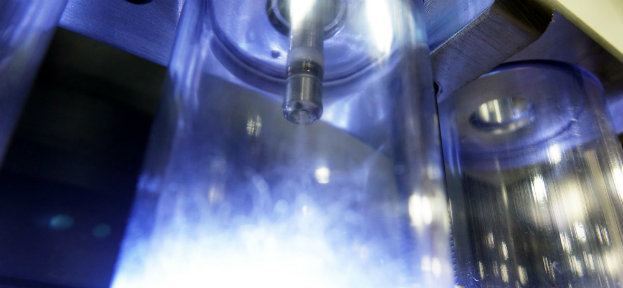
Gasoline Direct Injection moves fuel delivery directly to the point of combustion inside the cylinder and further refines the control engineers can exert over the air/fuel mixture. As a result, GDI equipped engines deliver yet again more power, better fuel economy, and improved emissions. GDI sounds like a panacea, but as with most new technologies, there are costs and risks.
Early GDI deployments experienced teething problems.
For example, gasoline direct injection nozzles are more robust than their predecessors because they must withstand the heat and pressure of the combustion chamber itself. Additionally, these nozzles are more refined than their MPFI cousins, further compounding the engineering and manufacturing challenge. More alarming for owners of early model GDI equipped vehicles, is that without precise injection mapping and control of the fuel plume inside the cylinder, combustion may be uneven and/or incomplete. This results in carbon buildup on the backsides of the intake valves which can occur rapidly, and repeatedly, with severe driveability and expense implications.
These issues have been largely addressed in current GDI equipped vehicles but for the aftermarket, they must be overcome if additional performance is to be achieved.
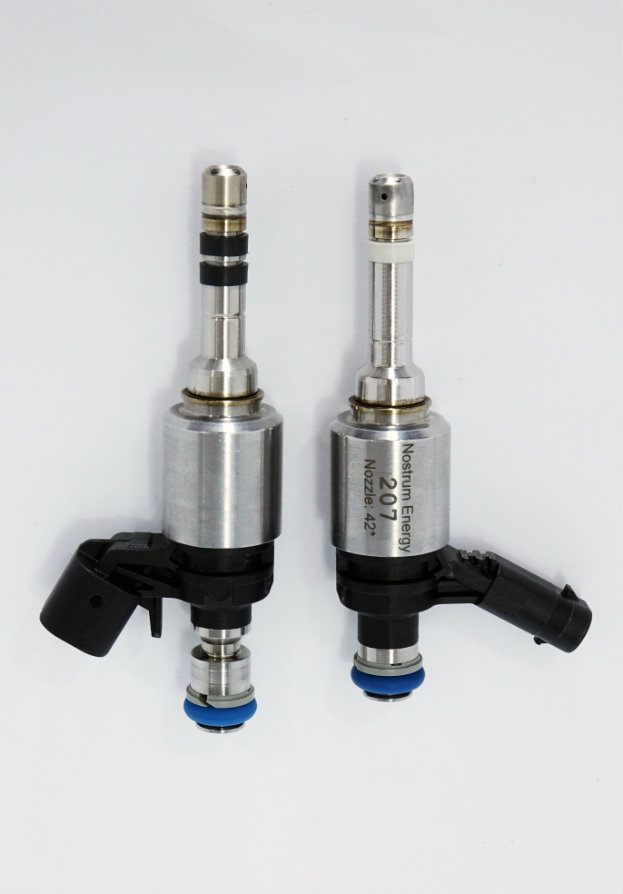
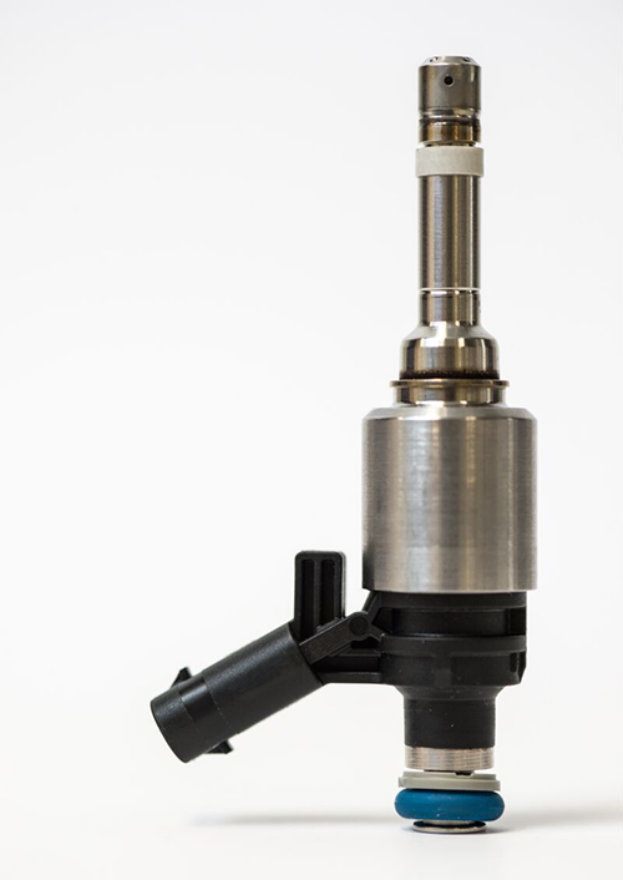
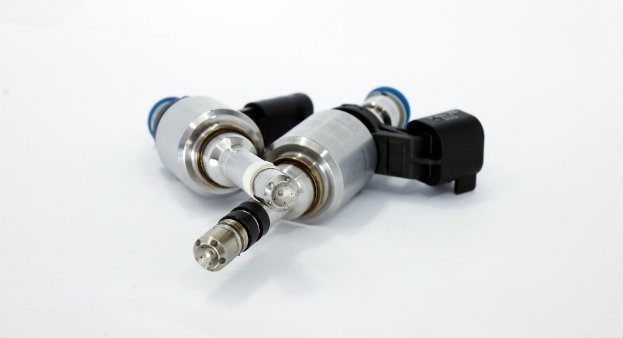
One challenge in performance oriented GDI systems is the need to introduce a greater volume of fuel into the cylinder in an exceptionally brief period of time, under tremendous pressure, without it hitting the opposite cylinder wall prior to combustion. This is not an issue with MFPI systems that introduce fuel upstream from the combustion chamber but in GDI, if fuel hits the opposite wall of the cylinder, combustion is uneven and carbon builds up on top of the intake valve.
The problem seems incremental, but the results are severe. VW GTI, Lexus IS 250, or Audi owners may be familiar with this pernicious, costly problem.
Just as aftermarket tuners elevate performance in SPFI and MPFI equipped vehicles simply by tuning the ECU, so too the aftermarket can tune the ECU in GDI equipped vehicles. An additional parallel in aftermarket performance tuning can be found in the injectors themselves. Vehicles can be tuned for additional output only as far as their hardware will allow. For example, highly tuned vehicles that receive upgrades to their air delivery, generally through forced induction, will eventually run into a fuel delivery constraint. To continue producing more power, these vehicles require high-flow, aftermarket injectors and for more extreme applications, high-flow fuel pumps.
The same constraint exists within GDI systems. For example, consumers who want their Cadillac ATS 2.0 to produce more than 450 horsepower will probably need more than a turbocharger upgrade. They will need to address their fuel delivery requirements, or suffer driveability consequences.
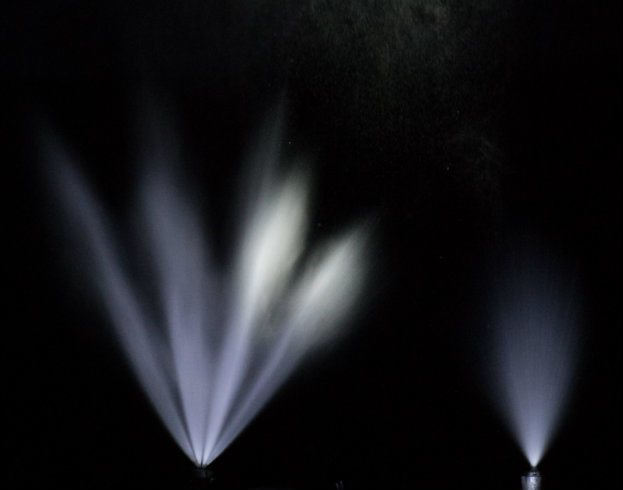
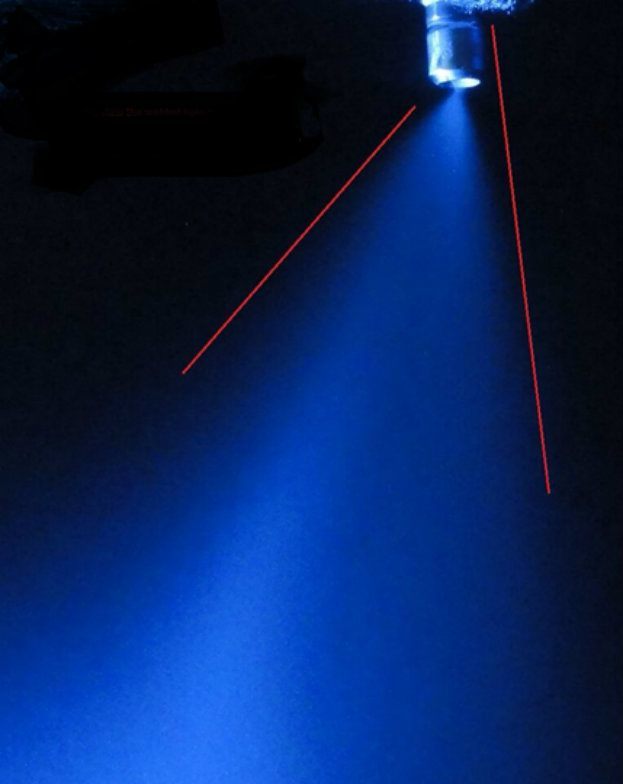
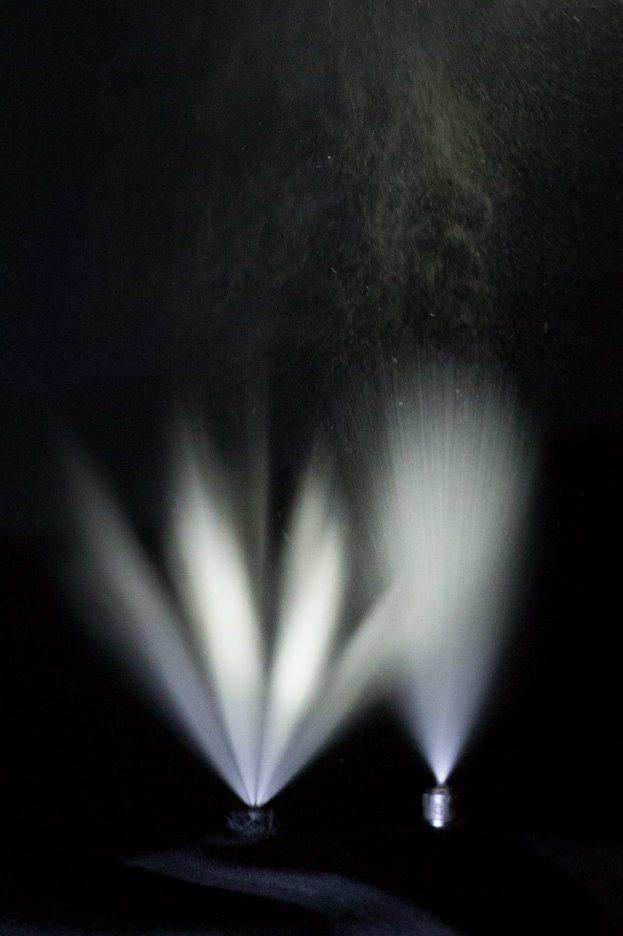
Nostrum Energy specializes in custom engineered fueling solutions and research. They work with universities, OEMs, Tier One suppliers, and race teams on advanced combustion solutions. In other words, they are working in highly demanding environments to develop solutions we may see adopted in production vehicles in 10 to 20 years. They are at the bleeding edge of GDI and water injection technologies, which has enabled them to build an intimate familiarity with the science of internal combustion.
Nostrum tried honing OEM GDI injectors to ease fuel flow. They tried adding additional holes to OEM injectors to let more fuel through. Neither of these produced the necessary results because they did not allow the precise management required in delivering a reliable, highly controllable increase in fuel delivery. The company spent three years developing a clean-sheet injector design that overcomes the obstacles to high-flow GDI. Their patented, kinetic particle break-up mechanism, branded High Flow K-DI, was inspired by the pharmaceutical industry.
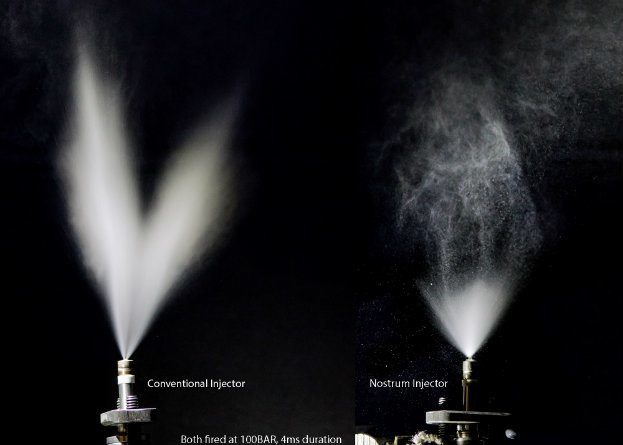
Nostrum is probably not going to be the low-cost solution. For example, tuning each GDI nozzle design requires more than 12 hours of computational time on a 36-core computer for each millisecond of injection time. And Nostrum’s GDI solution does not simply attempt to introduce more fuel than an OEM system. Their High Flow K-DI nozzles improve on OEM injectors by reducing droplet size and manipulating the direction and shape of the fuel plume, resulting in improved atomization and enabling shorter injection cycles.
Additionally, because their high atomization injectors burn more of the fuel introduced, they reduce the risk of carbon buildup.
In the first quarter of 2016, Nostrum will launch its High Flow K-DI GDI nozzles and associated hardware for GM Ecotec 2.0 powered vehicles. This is not your father’s 750 CFM carb or hand-held diesel tuner – you need a professional for the installation and integration. Nostrum is working through an undisclosed partner who is a leader in Ecotec tuning and understands how to utilize the nine 3D injector characterization tables provided with its GDI system. The company reports its injectors will likely be offered as part of a traditional, multi-stage tuning solution.
Although it will be expensive – each Michigan-made nozzle will run about $450 – the potential results are astounding. Nostrum will not commit to output details for the 2.0 Ecotec at this time, but they maintain that with complementary, hardware improvements and professional tuning, in excess of 500+ horsepower. Nostrum is well advanced in development solutions for other GDI equipped vehicles such as the Ford Ecoboost 2.0 and 2.3, and BMW N55 that powers the 335, 435, and 535.
The company is not well known in the performance aftermarket, but that may change.
Nostrum Energy plans to sell more than 2,000 units in 2016 and anticipates significant growth thereafter as their solutions become better known and new applications are launched. Nostrum will not have the performance aftermarket GDI space to itself forever, but if you are an early adopter with an Ecotec powered car who wants to embarrass exotics and big displacement muscle at the drag strip, keep an eye on Nostrum.
“Nostrum delivers highly-engineered, elegant solutions for high-flow GDI applications.” ~ Frank LoScrudato, Vice President of Development and Operations, Nostrum Energy.
*Seth Parks is an auto industry veteran, entrepreneur, and Seattle Seahawks fan.
Follow him on Twitter: @mseth_parks
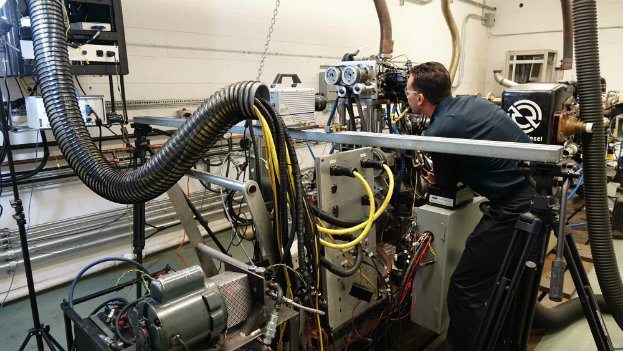
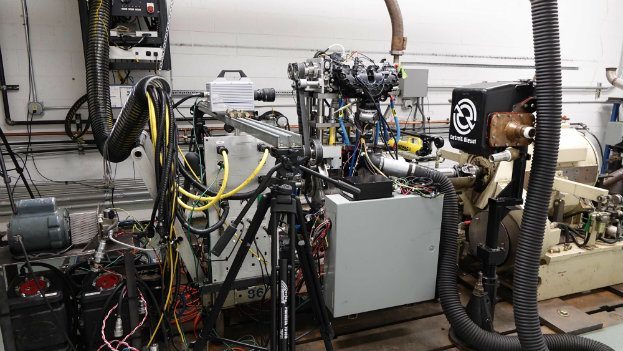
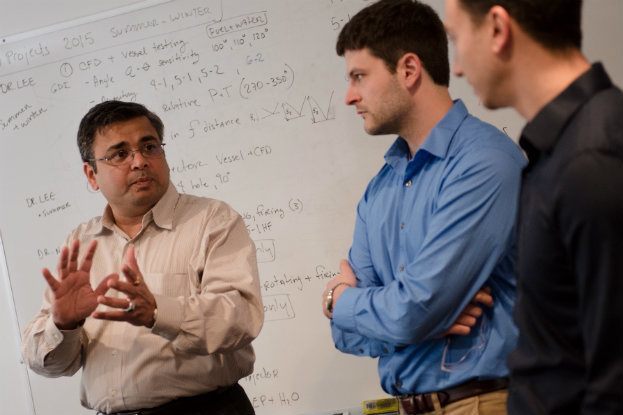
Cars have undergone tremendous changes and I’m very happy to see that consumers are getting what they want from automobiles. Innovative features are already included to make car ownership a lot more fulfilling.
This is fantastic! I’m happy to see that we are slowly but surely improving on this front. It drives me crazy (aha) to think that we are using the same basic technology that we were using 150 years ago on cars.